Intro to Rolling Mills
Rolling mills stand as pivotal equipment in metalworking, shaping countless materials into various forms with precision and efficiency. From transforming massive slabs into thin sheets to creating complex profiles, these machines are at the heart of manufacturing industries worldwide.
This guide delves into the intricate world of rolling mills, exploring everything from the fundamental principles and types of mills to the nuanced techniques of hot and cold rolling.
As we journey through the mechanics of metal deformation, we’ll uncover the robust designs and innovative technologies driving modern rolling mills. We’ll break down the hot rolled process, compare different roller mills, and dissect the anatomy of a mill roll to understand its vital role in metal shaping.
By highlighting the advantages and limitations of hot versus cold rolling, we aim to equip you with the knowledge to appreciate the art and science of metal rolling fully.
Join us as we explore the past, present, and future of rolling mill technology, uncovering the keys to efficiency, quality, and safety in metalworking operations.
The Basics of Rolling Mills
A rolling mill is a complex machine critical for shaping metals into desired forms, playing a pivotal role in metalworking industries. At its core, it utilizes rollers to apply force and deform metal sheets or ingots, altering their thickness and shape according to specific requirements.
The basic components include the main rollers that perform the deformation, a drive mechanism for moving the rollers, and a frame that supports the entire assembly.
Additionally, adjustments and control systems regulate the pressure applied and the speed of rolling, ensuring precision in the final product.
From simple manual mills in small workshops to highly automated systems in large-scale operations, the functionality of a rolling mill is foundational to achieving high-quality metal products used across various applications.
Contact us: service@drsengineering.ae for any equipment or service needs.
Understanding Hot Rolled Techniques

Hot rolling is a metalworking process where metal is heated above its recrystallization temperature and passed through rollers to achieve desired thickness or shape.
This technique is essential for producing larger quantities of metal sheets, bars, and rods with relatively lower costs compared to other processes.
The key benefits include enhanced ductility, allowing the metal to be formed and shaped more easily, and improved efficiency due to the reduced resistance of metal to deformation when hot.
Comparatively, hot rolling often results in a rougher surface finish than cold rolling, another common metalworking process where metal is shaped at room temperature.
While cold rolling can achieve tighter tolerances and a smoother finish, it requires more force and energy, making it less efficient and more expensive than hot rolling.
Moreover, hot rolled products generally have a significant advantage in structural applications where the material’s finish and precise dimensions are less critical but where the material’s ability to withstand external forces is paramount.
Also Read: Our Guide to the Forging Press
Roller Mill – The Workhorse of Metal Forming
Roller mills are pivotal in metal forming, functioning across various industries by applying precise pressure to deform metal into thinner gauges or specific shapes. There are several types, each tailored to different needs:
- Two-High Roller Mills: These are the most basic and widely used type, consisting of two opposing rolls between which the metal is passed. They’re versatile, used in both hot and cold rolling, and can be reversible for improved efficiency.
- Three-High Roller Mills: This type adds a middle roll, allowing for a reversal of the material without the need to flip the workpiece. This design enhances productivity and is often used in high-volume production.
- Four-High Roller Mills: Incorporating two smaller rolls within two larger ones, this mill provides tighter control over thickness, reducing the material’s thickness with greater precision. It’s particularly valuable for cold rolling applications where thin, uniform sheets are required.
- Cluster Mills (also known as Sendzimir mills): Feature multiple rolls stacked vertically to apply more pressure, ideal for very thin materials or materials requiring high precision.
In terms of innovation, modern roller mills incorporate advanced mechanical designs and materials that reduce maintenance needs, increase lifespan, and enhance efficiency. For example, the use of stronger, more wear-resistant materials for rolls extends their life and reduces downtime.
Technological advancements also include computer-controlled systems for precise adjustments and monitoring, ensuring uniform thickness and quality.
Furthermore, innovations in roller mill technology are focusing on sustainability and energy efficiency. Newer models are designed to consume less energy and incorporate recycling systems that minimize waste, aligning with the industry’s growing commitment to environmental responsibility.
These developments not only improve the metal forming process but also push the boundaries of what can be achieved, allowing for more complex shapes and finer materials to be produced more efficiently and sustainably.
The Art of Metal Rolling: A Step-by-Step Process
The art of metal rolling is a nuanced process, pivotal for transforming metal into varied thicknesses and shapes. Here’s a breakdown of the steps involved and key considerations for maintaining product quality and equipment integrity:
- Material Preparation: The process begins with preparing the metal, which may involve heating (in the case of hot rolling) to make it malleable. Ensuring uniform temperature distribution is crucial for consistent quality.
- Pre-rolling Treatment: This step might include applying a scale breaker to remove surface imperfections and employing lubricants to reduce friction between the metal and the rolls, protecting both the material’s surface and the machinery.
- Primary Rolling: The heated or untreated metal is passed through the main rolling mill, where it is compressed between two or more rolls to reduce its thickness. Uniform pressure application is vital to prevent material warping.
- Intermediate and Finish Rolling: These stages involve passing the material through additional sets of rolls for further thinning to the desired thickness and may include precise shaping processes. Attention to roll alignment and temperature control here is essential to maintain dimensional accuracy and material properties.
- Cooling and Coiling: After achieving the desired thickness and shape, the metal is cooled, either gradually in the air (for hot rolling) or rapidly (for cold rolling to set the metal’s microstructure), and then coiled for storage and transportation. Proper cooling techniques are important to prevent internal stresses and distortions.
- Post-rolling Treatments: The metal may undergo various treatments, such as temper rolling, annealing, or surface finishing, to enhance its mechanical properties or appearance. Consistent treatment processes ensure uniform quality across batches.
Quality and Machinery Considerations
Regular Inspection and Maintenance: Routine checks and maintenance of rolling mill components, especially rolls, bearings, and hydraulic systems, are essential to prevent unexpected downtime and ensure continuous, high-quality production.
Control System Upgrades: Implementing or upgrading to advanced control systems can enhance precision in roll gap adjustments, pressure application, and speed settings, directly influencing material quality and equipment efficiency.
Material Quality Control: Incoming material quality should be consistently monitored. Impurities or inconsistencies in the raw material can affect the rolling process’s efficiency and the final product’s quality.
Lubrication and Cooling Systems: Adequate lubrication and cooling of the rolls and material are vital to prevent wear and tear on the machinery and to control the metal’s properties throughout the rolling process.
Understanding and adhering to these steps and considerations are fundamental in mastering the metal rolling process, ensuring the production of high-quality materials while maintaining the longevity and efficiency of the rolling mill equipment.
Also Read: Understanding Valves and Pneumatic Systems
Anatomy of a Mill Roll
The “mill roll” sits at the heart of the metal rolling process, a pivotal component designed to apply pressure and shape metal as it passes through the rolling mill.
These cylindrical tools are responsible for the direct deformation of the metal, making their design, material, and integrity crucial for the efficiency, precision, and quality of the rolling process.
Materials
- Cast Iron: Widely used for its excellent wear resistance and thermal properties, making it suitable for high-temperature rolling processes.
- Steel: Offers superior strength and durability, with variations like high-chromium steel being preferred for their hardness and resistance to thermal cracking.
- Carbide: Used in composite rolls, where carbide inserts are embedded into a steel roll body, providing exceptional hardness and wear resistance for cold rolling applications.
- Ceramic: Though less common, ceramic rolls are utilized in specialized rolling processes where high wear resistance and the ability to withstand extreme temperatures are necessary.
Designs
- Smooth Rolls: Primarily used for flat products, these rolls rely on their smooth surface to ensure uniform thickness and surface finish.
- Grooved Rolls: Designed with grooves of various shapes to facilitate the rolling of rods, bars, and structural shapes, allowing for precise control over product dimensions.
- Textured Rolls: These rolls have specially designed surfaces to impart desired textures on the metal surface for aesthetic or functional purposes.
Each material and design caters to specific rolling needs, influenced by factors such as the type of metal being rolled, the rolling temperature, the required surface finish, and the mechanical properties desired in the final product.
For instance, rolls made from high-chromium steel or carbide composites are often chosen for their ability to maintain high precision in dimension control and surface finish in cold rolling applications, where material hardness significantly increases.
Selecting the appropriate mill roll for a given application involves considering the rolling process’s specific requirements, including the metal type, rolling speed, temperature conditions, and the desired characteristics of the finished product.
By carefully matching the mill roll’s material and design to these factors, manufacturers can optimize the rolling process for efficiency, quality, and equipment longevity, ensuring that the rolling mill operates at its full potential.
Cold Rolling vs. Hot Rolling: Advantages and Limitations
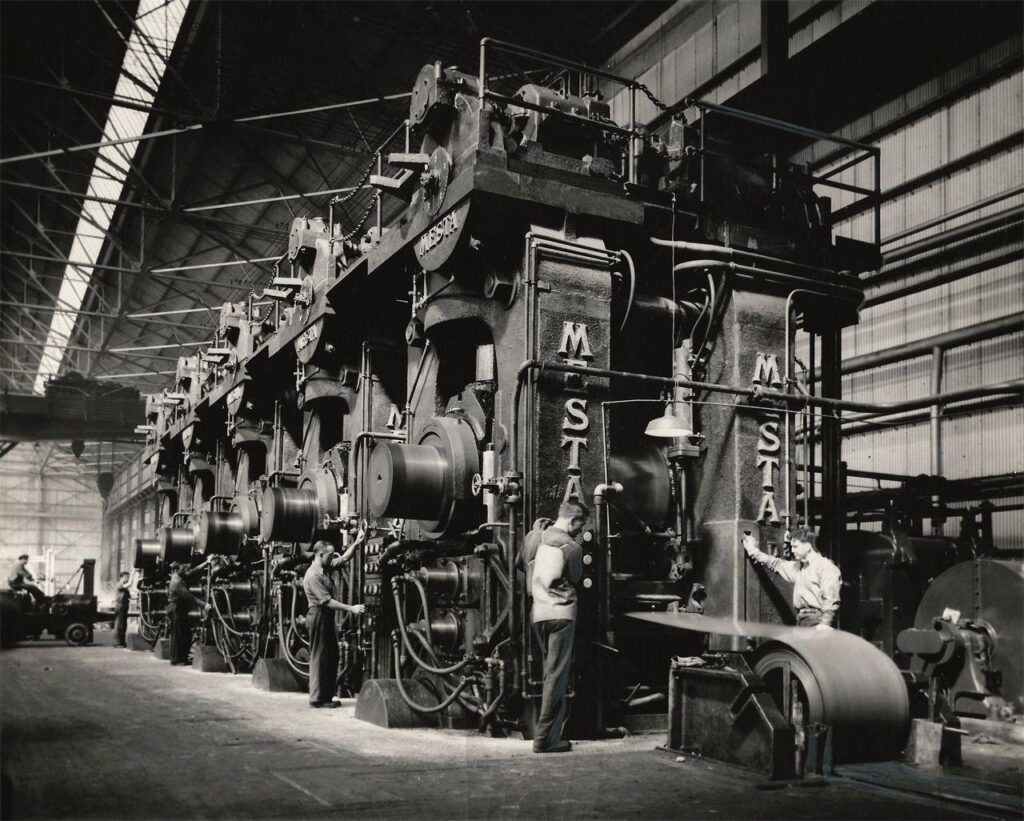
Hot Rolling
This process involves rolling the metal at high temperatures, above its recrystallization temperature. It’s the first step in metalworking, creating a product that can be further refined.
Advantages of Hot Rolling
- Efficiency: Hot rolling is typically faster and requires less energy for the metal to deform.
- Workability: The high temperatures make metals easier to shape and form into large sizes.
- Cost-effective: Generally less expensive due to fewer processing steps.
Limitations:
- Rough Surface: The process often leaves a scale, leading to a rough surface finish.
- Dimensional Precision: It offers less control over the final dimensions due to the metal’s tendency to expand and contract upon cooling.
Cold Rolling
Occurs at or near room temperature, further refining products created by hot rolling to enhance surface finish, increase strength, and improve dimensional precision.
Advantages of Cold Rolling
Surface Finish: Produces a smoother surface without the scale found in hot rolling.
Increased Strength: Through work hardening, the metal becomes stronger than when hot rolled.
Tight Tolerances: Offers greater control over dimensions and thinner gauges.
Limitations
- Material Hardness: Not all metals can undergo cold rolling due to increased hardness and potential for cracking.
- Cost: Generally more expensive due to additional processing and the need for more powerful equipment.
When to Use Each Method
Hot Rolling is preferred when large quantities of steel need to be produced, and surface finish is not a primary concern, such as in the construction industry for structural components.
Cold Rolling is chosen for applications requiring high tolerance, smooth surface finishes, and enhanced strength, like in the automotive and aerospace industries for parts and panels.
The selection between hot and cold rolling ultimately depends on the project requirements, including the desired material properties, cost considerations, and the end product’s application.
Each process offers unique advantages and limitations, making them indispensable in their respective applications within the metalworking industry.
Maintenance and Safety in Rolling Mill Operations
Best Practices for Maintenance
- Regular Inspections: Routine checks of machinery and components to identify wear and potential failures early.
- Lubrication: Ensure all moving parts are adequately lubricated to reduce friction and wear.
- Cleaning: Keep the equipment and work environment clean to prevent build-up that can lead to equipment malfunctions.
- Calibration: Regularly calibrate machines to ensure they operate within specified parameters for optimal performance.
- Record Keeping: Maintain detailed records of maintenance, repairs, and replacements to track equipment health over time.
Safety Protocols
- Training: Comprehensive training for all operators on machine operation, safety practices, and emergency procedures.
- Personal Protective Equipment (PPE): Mandatory use of PPE, such as gloves, safety glasses, and hearing protection.
- Machine Guards: Use of guards and barriers to protect operators from moving parts and flying debris.
- Emergency Stops: Ensure emergency stop buttons are accessible and functional to quickly halt operations if needed.
- Fire Safety: Implement fire safety measures, including extinguishers, fire blankets, and clear evacuation routes.
Maintenance and safety in rolling mill operations are intertwined, ensuring both the longevity of equipment and the well-being of personnel. Adhering to best practices for maintenance not only preserves the machinery for optimal productivity but also minimizes the risk of accidents.
Safety protocols are paramount to creating a secure work environment, significantly reducing the likelihood of injuries. By prioritizing these aspects, facilities can maintain high efficiency while safeguarding their most valuable asset: their workforce.
Future Trends in Rolling Mill Technology
Automation and AI Integration
- Predictive Maintenance: Leveraging AI to predict equipment failures before they occur, significantly reducing downtime.
- Quality Control: AI-driven analysis of product quality in real-time, adjusting the process variables automatically to ensure consistent output.
- Process Optimization: Automation technologies optimizing rolling schedules and sequences, enhancing productivity and reducing energy consumption.
Sustainable Practices and Energy Efficiency
- Recycling and Waste Reduction: Advanced technologies enabling higher recycling rates of metal scraps, reducing waste and raw material usage.
- Energy Recovery Systems: Implementation of systems to recover and reuse heat energy lost during the rolling process, improving overall energy efficiency.
- Renewable Energy Sources: Increasing adoption of renewable energy sources, such as solar and wind power, to operate rolling mills, reducing carbon footprint.
The future of rolling mill technology promises significant advancements through automation, AI integration, and sustainable practices. These innovations aim not only to enhance efficiency and product quality but also to minimize environmental impact.
By embracing these trends, the metalworking industry can look forward to more intelligent, efficient, and eco-friendly production processes, setting a new standard for manufacturing excellence.
Contact us: service@drsengineering.ae for any equipment or service needs.
Concluding our post on Rolling Mills
Rolling mills stand as pivotal tools in the metalworking landscape, adeptly transforming raw metal into forms vital for countless applications.
From the intricacies of hot and cold rolling processes to the precision of mill roll designs and the robust capabilities of roller mills, these machines embody the blend of strength and finesse required for metal forming.
Innovations in technology, particularly in automation and sustainable practices, promise a future where efficiency and environmental responsibility go hand in hand.